Common malfunctions of Hammer
- excavator spare parts
- Jan 30, 2019
- 3 min read
Operation errors, nitrogen leakage of the breaker, improper maintenance and other phenomena can cause failures in the working valve of the breaker, bursting of the pipeline, and local overheating of the hydraulic oil. The reasons are: first, the technical configuration is unreasonable, and second, the site management is improper.
The working pressure of the breaker is generally 20 MPa and the flow rate is about 170 L/min. The system pressure of the excavator is generally 30 MPa, and the flow rate of the single main pump is 250 L/min. Therefore, the relief valve has to bear heavy shunt unloading work. Once the overflow valve is damaged but not easy to be detected, the breaker is working under ultra-high pressure. The first is the burst of the pipeline and the local overheating of the hydraulic oil. The next step is the severe wear of the main reversing valve and the other main working valve of the excavator. The hydraulic circuit controlled by the spool (the next spool to which the main oil passage is directed at the neutral position) is contaminated; and because the return oil of the breaker is generally not passed through the oil filter to the tank without passing through the cooler, the circulation oil path may be The oil temperature of the working oil circuit is too high or even too high, which seriously affects the service life of hydraulic components (especially seals).
Troubleshooting
The most effective way to prevent these faults is to improve the hydraulic circuit. First, add an overload valve at the main reversing valve (optional with the same type of overload valve equipped with the boom or bucket working valve), the setting pressure should be 2~3MPa larger than the relief valve, which can effectively Reduce the impact of the system, while ensuring that the pressure of the system is not too high when the overflow valve is damaged; the second is to connect the oil return line of the working oil line to the front of the cooler to ensure timely cooling of the working oil return; third, when the main pump flow exceeds the maximum of the broken hammer When the flow rate is twice, install a diverter valve in front of the main reversing valve to reduce the load on the relief valve and prevent overheating caused by a large amount of oil supply through the relief valve. Practice has proved that the improved EX300 excavator (old machine) with KRB140 hydraulic breaker has achieved good working results.
Cause of failure and correction
First, not working
1. The nitrogen pressure in the hind body is too high. ------ Adjust to standard pressure.
2. The oil temperature is too low. Especially in the winter in the north. ------- Increase the heating settings.
3. The shutoff valve is not open. ------Open the shutoff valve.
4. Insufficient hydraulic oil. --------Add hydraulic oil.
5, the pipeline pressure is too low ------- adjust the pressure
6, the pipeline connection error ------- correct connection
7. There is a problem with the control line ------ check the control line.
8, the reversing valve is stuck ------- grinding
9, the piston stuck ------ grinding
10, the drill rod and the flat pin are stuck
11, the nitrogen pressure is too high ------ adjusted to the standard value
Second, the impact is too low
1. The working pressure is too low. Insufficient flow ------ adjust pressure
2, the body nitrogen pressure is too low -------- adjust the nitrogen pressure
3, high pressure nitrogen pressure is insufficient ------ added to standard pressure
4, the reversing valve or piston pulling or excessive clearance ------ grinding or replacement
5, poor oil return ------ check the pipeline
Third, the number of strikes is insufficient
1. The nitrogen pressure of the rear body is high ------ adjust to the standard value
2, the reversing valve or piston pulling ------ grinding
3, poor oil return ------ check the pipeline
4, the system pressure is too low ------ adjust to normal pressure
5, the frequency regulator is not adjusted ---- adjust
6, hydraulic pump performance is low ------- school oil pump
Fourth, abnormal strike
1. Can not be hit when pressed, and can be hit when lifting a little bit ------ inner wear. replace
2, when the time is fast -----clean the inside of the hydraulic hammer. Sometimes grinding valves or pistons
3, the performance of the hydraulic pump is also low - this school oil pump
4, the drill rod is not standard ---- replace the standard drill rod
Fifth, the pipeline transition vibration
1, high pressure nitrogen pressure is too low ------ added to the standard
2, the broken bowl ------ replacement
3, the pipeline is not clamped ------ re-fixed
Sixth, oil leakage ------ replace the relevant oil seal
Seven, leaking ------ replace the gas seal. https://jnjmzm.wixsite.com/sdjygcjx
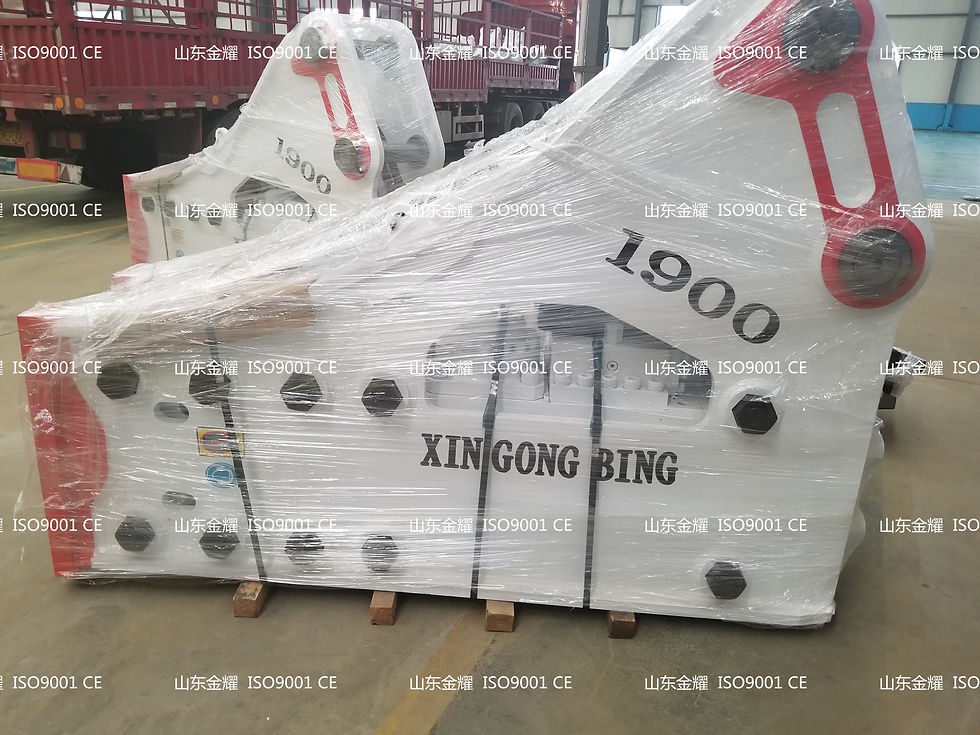
Comments